A Comprehensive Overview to Executing Foam Control Solutions in Your Procedures
Efficient foam control is a vital element of operational effectiveness that commonly goes overlooked. Understanding the ins and outs of foam generation can substantially impact both productivity and product quality. This guide outlines the numerous challenges positioned by foam and the diverse services readily available, giving a structure for picking and carrying out one of the most ideal strategies. By checking out key elements such as application compatibility and workers training, organizations can optimize their foam management efforts. As we explore these components, the possibility for transformative renovations in your procedures comes to be noticeable. What actions will you take following?
Understanding Foam Challenges
Foam obstacles are a substantial worry throughout different markets, impacting functional efficiency and item quality. The formation of too much foam can impede processes such as mixing, transport, and storage, leading to raised downtime and waste. In industries like food and beverage, drugs, and petrochemicals, foam can interfere with assembly line, triggering product incongruities and contamination threats.
In addition, foam can obstruct tools performance, bring about expensive repairs and upkeep. In wastewater treatment, foam can interfere with clarifier operations, resulting in lower therapy effectiveness and governing conformity issues.
Recognizing the underlying reasons for foam generation is critical for effective management. Factors such as surfactants, temperature level variations, and frustration levels can all add to foam manufacturing. Identifying these aspects permits markets to implement targeted approaches that minimize foam formation while preserving item stability.
Kinds of Foam Control Solutions
Mechanical options include making use of devices such as foam skimmers or defoamers. These tools literally get rid of foam from the surface of liquids, consequently preventing overflow and keeping ideal degrees in reactors and storage tanks. Chemical remedies, on the other hand, consist of the application of defoaming representatives-- materials that interrupt the foam structure, bring about its collapse. These agents can be silicone-based, organic, or liquid, each offering distinct advantages depending upon the application setting.
Lastly, operational methods concentrate on procedure changes. This might involve changing tools parameters, such as temperature level and stress, or transforming the circulation prices of liquids to reduce foam generation. Additionally, executing great housekeeping methods can also alleviate foam formation by reducing contaminants that add to foam security.
Selecting the appropriate foam control remedy entails examining the particular requirements of the operation, consisting of the kind of process, the features of the materials involved, and security considerations.
Picking the Right Products
Choosing the appropriate foam control items needs a detailed understanding of the certain application and its distinct obstacles. Aspects such as the kind of foam, the environment in which it happens, and the desired end result all play critical roles in product option. Foam Control. In markets such as food processing, it is critical to choose food-grade defoamers that comply with security regulations while efficiently managing foam.
In addition, consider the thickness of the liquid where the foam issue exists. Some items are created for low-viscosity applications, while others are tailored for thicker liquids. Compatibility with existing processes is one more critical aspect; the chosen foam control representatives should integrate flawlessly without disrupting general operations.
Another vital variable is the method of application. Some products may require dilution, while others can be used directly. Assessing the simplicity of usage and the needed dosage can offer understandings right into the item's efficiency and cost-effectiveness.
Application Approaches
Effective execution techniques for foam control remedies require a methodical technique that lines up product choice with functional needs. The initial step involves a complete evaluation of the procedures where foam takes place, determining certain locations that necessitate intervention. By involving cross-functional groups, consisting of quality, manufacturing, and design assurance, organizations can collect understandings that notify the selection of one of the most reliable foam control products.
Next, it is critical to develop clear goals for foam decrease, making certain that these objectives are achievable and quantifiable. This might entail defining appropriate foam degrees and the timelines for implementation. Educating personnel on the buildings and application techniques of selected foam control representatives is equally vital, as correct use is important for optimal outcomes.
Additionally, incorporating foam control solutions right into existing process needs careful preparation. Organizations should develop a phased implementation plan, permitting modifications based upon initial outcomes. Regular communication and responses loops with team associated basics with the procedure will help with timely problem-solving and cultivate a culture of continuous enhancement. Inevitably, a well-structured technique will certainly enhance functional effectiveness while effectively handling foam-related obstacles.
Surveillance and Examining Performance
Surveillance and evaluating the efficiency of foam control options is essential for guaranteeing that carried out approaches yield the desired results. This procedure includes organized information collection and analysis to evaluate the performance of foam control representatives and strategies. Key performance indicators (KPIs) need to be developed prior to implementation, enabling a clear standard versus which to gauge progression.
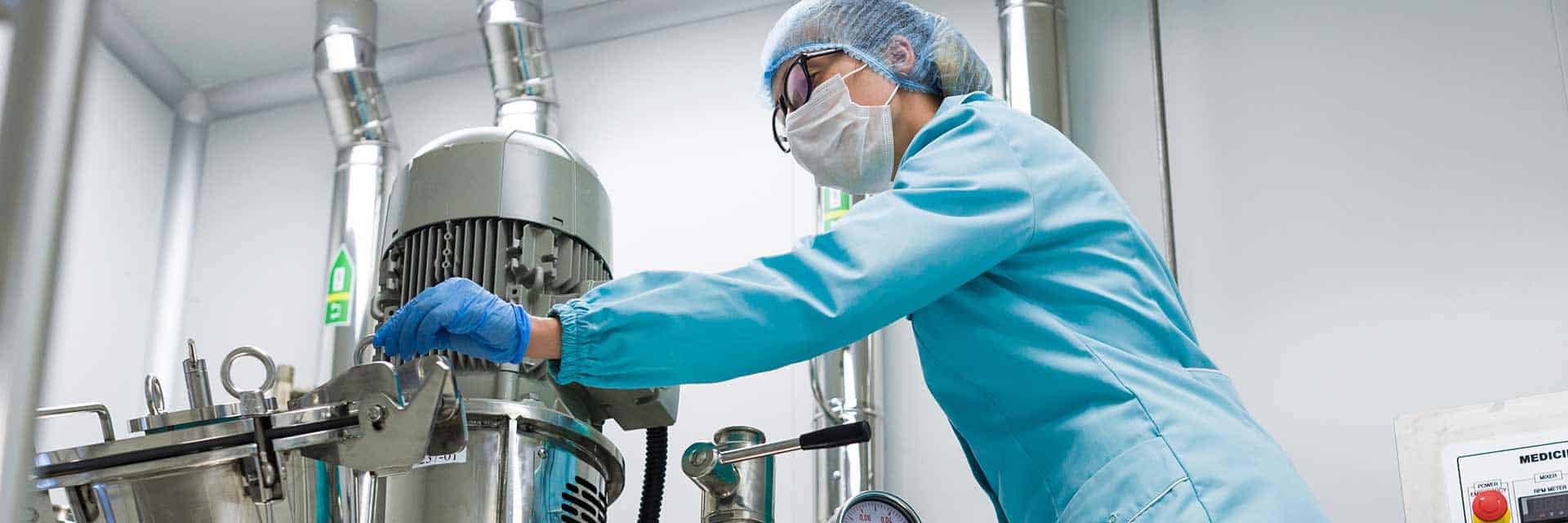
Assessing effectiveness likewise needs regular reviews of foam control treatments and agent efficacy. This can be achieved via sampling and screening, enabling operators to establish if existing services are fulfilling operational needs. It is critical to get feedback from team participants who interact with these systems daily, as their understandings can reveal operational nuances that measurable information may forget.
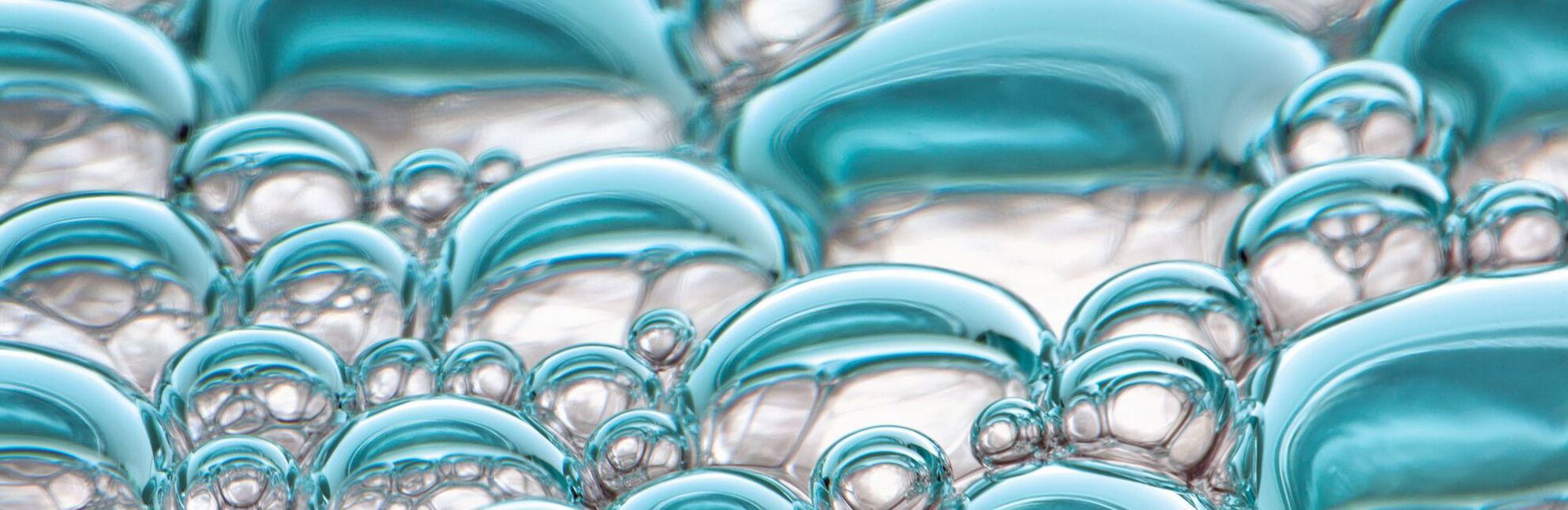
Ultimately, an organized monitoring and assessment framework helps identify necessary changes, guaranteeing that foam control services stay effective, cost-effective, and straightened with business objectives.
Final Thought
Finally, effective foam control solutions are vital for enhancing operational performance and keeping item quality. An extensive understanding of foam difficulties, combined with the choice of proper items and implementation approaches, assists in the successful administration of foam generation. Establishing measurable KPIs and spending in employees training better boost the performance of foam control procedures. Routine monitoring and analysis make certain continuous improvement, ultimately bring about a much more efficient and structured operational environment. discover this
Applying good housekeeping techniques can also alleviate foam development by decreasing pollutants that add to foam stability.
Picking the best foam control items calls for a complete understanding of the specific application and its distinct obstacles (Foam Control).Successful application methods for foam control solutions require a systematic strategy that straightens item selection with operational requirements.In final thought, efficient foam control solutions are necessary for maximizing functional performance and maintaining product top quality. A comprehensive understanding of foam difficulties, integrated with the choice of proper items and application approaches, facilitates the successful monitoring of foam generation